All the combustion pressure and boost int he world is useless if you can't seal it. JE's Pro Seal MLS gaskets are an evolution in headgasket design.
Stepping up to Pro Seal MLS head gaskets from the composite or graphite units that are standard equipment on many factory engines is a good idea—if only because this trend is being validated by more automakers offering MLS gaskets on select high-performance engines in their lineups. Also, all NASCAR and Pro Stock teams use MLS gaskets as composite fell out of favor and solid copper gaskets were not effective in sealing fluids.
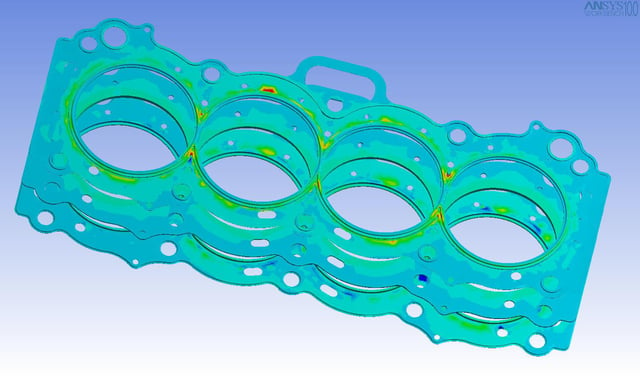
An abbreviation for multi-layer steel, MLS gaskets have taken center stage in the shop due to a number of engine-builder-friendly features. Granted, they can be a bit more expensive that conventional gaskets, however, the performance and durability advantages will pay off in the long run.
“JE Pro Seal gaskets differ greatly from OEM gaskets,” said Jeremy Anderson of JE Pistons. “JE Pro Seal gaskets have a proprietary outer layer coating that prevents them from sticking to the deck surfaces. Our gaskets go through a heat treating and tempering process which gives them a memory, and makes the gaskets want to
The basic premise of a MLS gasket is sandwiching three or more layers of thin steel that have been embossed in critical sealing areas. The embossments act as “springs” to ensure that there is no leakage of fluids or combustion pressure if the cylinder head moves or expands while the engine is under heavy load. The gaskets can also be coated to improve sealing in “micro” areas between the block, head and gasket.
Need A Set of Pro Seal Gaskets? See All Available Applications HERE
There are different theories with regards to the number of steel layers and the types of coatings, along with the embossment design and construction method—which is the most critical to the sealing operation.
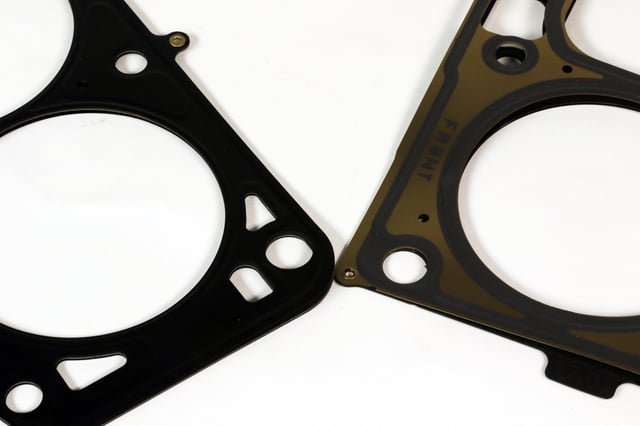
The embossment design, placement, and multi-step pressing process topple our competitors,” says Anderson. The Pro Seal design philosophy starts with three layers of a 304 stainless steel.
“Having all layers stainless, and the same material allows for a gasket that is made of quality, consistent material, and has the same expansion properties—which is one aspect that allows for an improved gasket seal,” explains Anderson. “The layer thickness and amount of layers are dictated by the required gasket thickness for the specific application.”
Some gasket manufacturers start with coated sheets of steel. Pro Seal starts with raw stainless steel that is laser cut to the proper dimensions. This strategy helps facilitate a multi-step forging that shapes the embossments to the desired contours.
“The multi-step embossing allows for the embossments to be created without too much material stresses focused all at once,” says Anderson. “The smooth formation of embossments are always placed with the final use and bore size in mind. Every bore size has its own tool so that the fire ring embossment always retains the same distance away from the edge of the bore for each bore size available.”
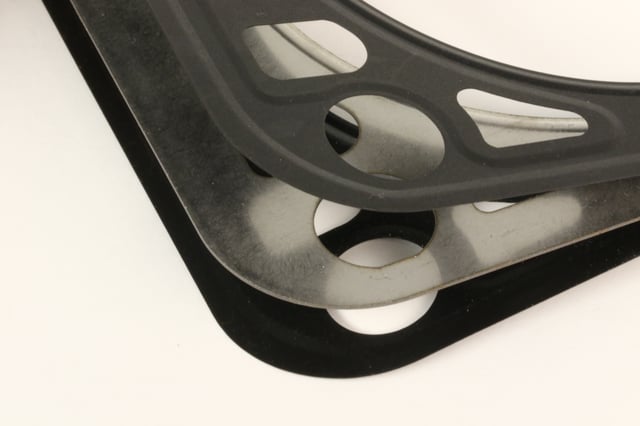
The “smooth formation,” as noted in the accompanying illustration, differs from some competitors that utilize a harsher stamping approach. This action can result in sharp peaks in the embossment that can generate stress cracks.
Following the embossment, the steel layers are heat treated and tempered so that the gasket retains its shape and won’t flatten back to its original shape under pressure.
These design and construction elements are examples of why MLS is quickly being preferred over composite gaskets, which start out as a basic metal core with a pliable material such as asbestos applied to both sides. Asbestos was soon rejected in favor of less hazardous composites but the design tactics were the same: use a material that easily conforms to the imperfections of the block and cylinder heads surfaces. A flange or “fire ring” is then installed around the bore opening to retain cylinder pressure. Other types of sealant may then be applied around fluid openings, but the fire ring is still basically a separate element that has to be fixed in position on the gasket. In contrast, each layer of a MLS gasket is a single unit with the embossments acting together to perform the same function as the fire ring when the gasket is compressed.
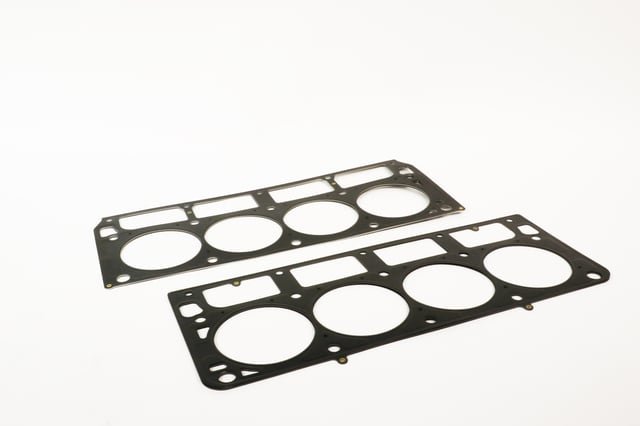
Pro Seal employs an even more effective fire-ring strategy that folds over the edge of the middle steel layer to form a “gas stopper” blockage point completely around the combustion chamber. When compressed, that extra metal allows the head and block to clamp together more tightly to prevent gas leaks. This design is especially effective in high-boost applications where the cylinder head may actually lift up slightly from the block. Even the smallest of gaps will create a significant pressure leak. The spring characteristics of a MLS gasket will fill that gap whereas a composite or graphite gasket has to expansive or elastic properties to the control leakage in those high-boost situations.
“The gas stopper feature also avoids distortion of the components, thanks to their more rapid temperature stabilization,” adds Anderson.
Once the stainless steel layers are embossed and tempered, they are individually coated with a proprietary process, which includes a primer, rubber-like Viton coating, and finally a silicone-based compound that helps release the gasket during engine disassembly. That’s another advantage over a conventional graphite gasket that often needs a scraper to remove and plenty of rags to keep the debris out of the cylinders.
By applying the coatings last, the entire gasket is covered, including fluid holes. With no exposed steel, there’s high resistance to corrosion.
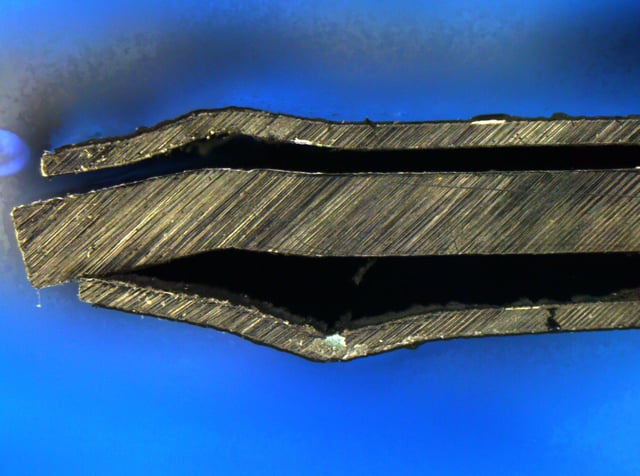
There is one caveat to using MLS gaskets that must be observed closely. The surface finishes of the block deck and cylinder head must be smooth enough to meet the Pro Seal requirements. Automakers already have highly sophisticated machining operations that leave factory blocks smooth enough to support MLS gaskets. This stipulation can often require working with a machine shop that has a profilometer to measure surface roughness.
The sealing surfaces should be free of scratches, scuff marks, local corrosion or cracks to avoid leakage. Following are suggested maximum values on the sealing surfaces:
- Rz 11µm
- Rmax 15µm
- Wt 8 -10µm
“The values can be measured with a surface finish probe” says Anderson. “The following Ra values are almost equivalent to the previous values achieved with equipment such as Rottler, Robbi or Serdi: Ra 0.8 μm for vertical processing (with cutting tips), Ra 1.6 μm for surface grinding.”
Pro Seal also has maximum out-of-flatness suggestions. Using a straight edge to level and thickness gauge, the maximum distance in the longitudinal direction is:
- Length of 100 mm, maximum 0.03 mm
- Length of 400 mm, maximum 0.05 mm
“The maximum cross-machine distance for a length of 100 mm is 0.03 mm,” adds Anderson. “In general, it’s best to have the flattest surface seal possible to ensure the gasket’s highest hermetic sealing capacity.”
One question often asked about MLS involves multiple use. The safest answer is no, MLS gaskets can lose sealing ability once the embossments are crushed. But in many real-world scenarios there have been examples where the gasket functioned as needed. The key is close inspection of the coating surfaces for any scratches or scrapes.
“We have customers that have had to remove the cylinder head for inspection at the race track and have re-used our gaskets,” says Anderson. “The reality is that the cost of the gasket would not be worth doing this unless it was an emergency and a replacement was not available.”
Old-school installation techniques—such as applying some type of sealing spray before positioning the gasket on the block—won’t work with MLS gaskets because the ingredients in the sealer may have a negative effect on the gasket coatings.
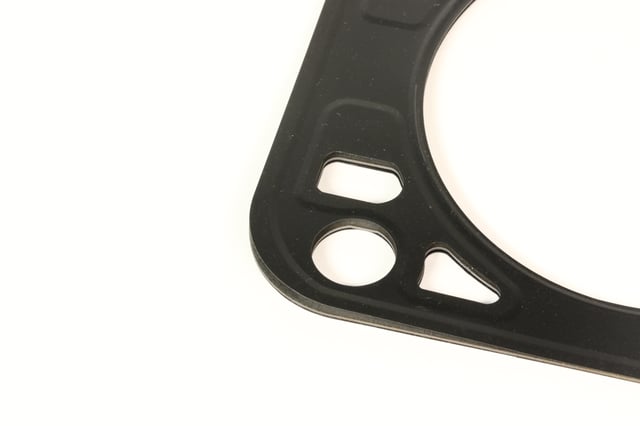
“We do not suggest using any type of copper spray, sealer, or the use of block or head O-rings,” cautions Anderson. “If O-rings are used, be sure to place the O-ring outside of the fire ring embossment.”
Pro Seal offers its MLS gasket line for most popular engines, both domestic and import. Many applications come in different bores and compressed thickness. When required, left- and right-side gaskets are provided.
For now, the future of sealing the block and head on most high-performance and racing applications is the MLS gasket. Continued improvements in construction and design will increase the pressure levels these gasket can withstand, and improvements in fasteners and clamping procedures will also drive the acceptance rate.