It might be hard to accept, but it’s true - the ubiquitous LS engine platform is 20 years old. Today, GM’s Gen III/IV small block V8 can be found between the fenders of everything from resto-mod muscle car classics to drift-beater Nissans, and it’s generally regarded as essentially bulletproof. What we don’t usually remember is that when it made its debut in the 1997 Corvette, a clean-sheet redesign of Chevy’s flagship sports car, it almost immediately drew criticism for one particular flaw; The LS1 tended to be noisy on cold startup.
To be fair, some of this issue can be laid at the feet of the buyers, since the new Corvette purchaser demographic tends to be more sensitive to noise, vibration, and harshness (NVH) issues than your average Chevy customer, but it was serious enough to lead GM to pursue a number of remedies, ranging from different recommended oil viscosity all the way up to warranty engine replacement.
So what led to the noise a small but significant number of owners experienced? Though there are a number of potential sources for startup noise, a phenomenon known as “piston slap” is to blame. The LS1’s combination of an aluminum block and lightweight pistons with short skirts designed to improve fuel economy and reduce friction teamed up with cold piston-to-cylinder tolerances to create unwanted noise.
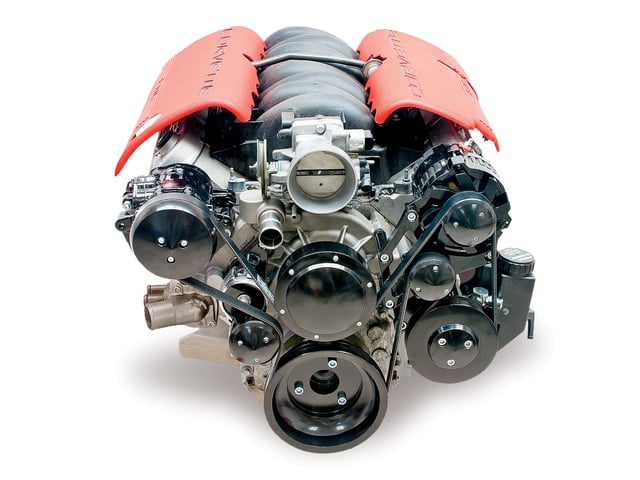
Piston Slap Explained
“Piston slap is generally caused when the cold running clearance (piston-to-wall clearance) is large enough that when the piston rocks from side to side in the bore it “slaps” the side of the cylinder and causes noise,” explains JE Pistons’ Clayton Stothers. In the case of the LS, the shorter piston skirt meant that the angular shift of the piston in the bore was more pronounced than with a longer piston running the same clearance. To make matters worse, that clearance couldn’t be tightened due to the fact that even with cast-in iron sleeves, the early, aluminum LS block wasn’t as dimensionally stable as an all-iron small block Chevy.
Though the LS1 is one of the best known examples of factory engines known for piston slap, it’s a common issue for many other high performance designs. Per Stothers, “Certain block designs will transmit the noise much easier than other blocks, and newer aluminum blocks are particularly susceptible. One that comes to mind for me is the VR38DETT Nissan GT-R engine. It is an aluminum block with a very thin (0.15mm) plasma-sprayed steel liner so it tends to expand at a similar rate to the piston. This would cause piston noise because the cold clearance would never really tighten up, even at operating temperature.”
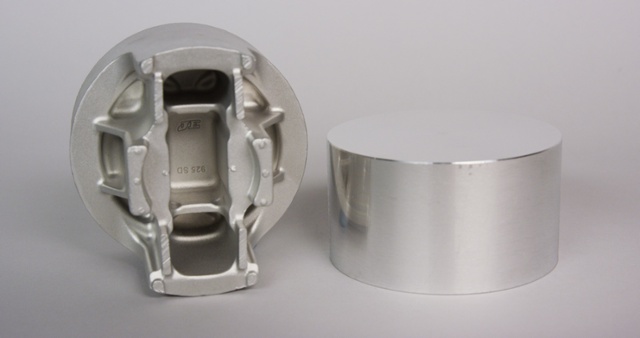
In high performance aftermarket applications, piston slap can also become prominent. JE Pistons recommends an additional 0.001 to 0.003 inch additional piston-to-bore clearance for supercharged, turbo, nitrous, and endurance engines, which can make for more noise on startup especially when combined with the wider tolerance required for high performance forged 2618 alloy slugs. “We need to provide more clearance for 2618 since it expands more than other alloys,” Stothers explains. “Also, high power engine builders need to provide more clearance to account for their power level so that also adds to the noise.”
Sound Solutions
Controlling or eliminating piston slap begins by understanding exactly what’s going on between the piston and the cylinder bore that causes it. According to Stothers, “The reason pistons with more cold clearance make more piston slap noise is that when the piston moves from the minor thrust side to the major thrust side at TDC, it can gain more velocity before striking the cylinder wall. More clearance means that the piston has more distance to gain velocity and it contacts the cylinder with more force than if it had less clearance.” As we noted earlier, a longer skirt will resist this effect by limiting the rocking angle, and other design choices like an offset pin location can also have an influence on piston slap, but compromises like these aren’t the best solution.
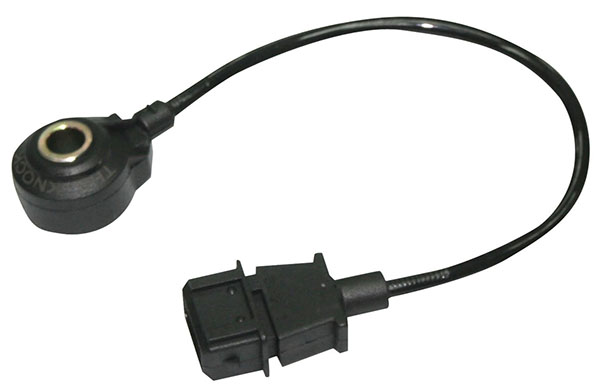
“An offset pin will help to reduce the noise by changing the motion of the piston and help reduce the force at which it hits the cylinder bore,” Stothers admits, but counsels against trying to solve the problem by trading away other desirable characteristics. “The skirt shape (cam and barrel) is focused on providing good running properties while the engine is warm and we don’t make sacrifices in order to reduce cold startup noise.”
“The primary contributing factor is clearance to the bore, so if you are able to tighten that up you will see a reduction in noise,” Stothers adds. Unfortunately, a certain amount of excess cold bore clearance is a necessary evil, especially in engines with 2618 alloy pistons, aluminum blocks, or power adders. The solution developed by JE is a unique coating designed to dynamically conform to the bore, effectively ‘taking up the slack’ and stabilizing the piston in the cylinder without compromising the necessary metal-to-metal tolerances required.
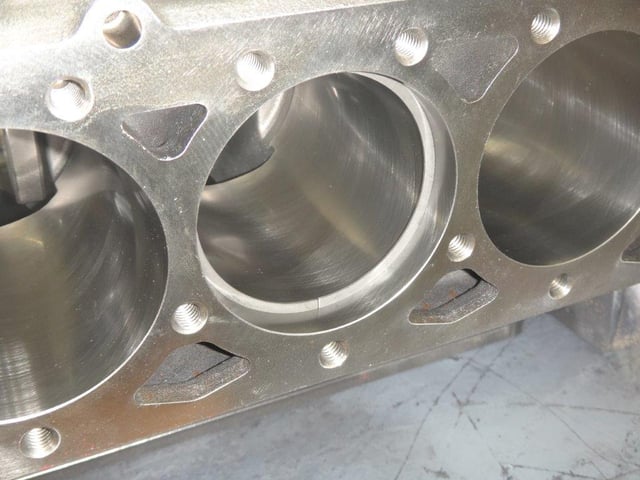
Patented Perfection
JE’s patented Perfect Skirt coating isn’t like typical skirt treatments that are intended as a temporary break-in layer. “Perfect Skirt works by permanently bonding a solid film lubricant to the bare aluminum in a relatively thick layer,” Stothers explains. Rather than being sprayed, the solvent-based coating is screen-printed to the skirt and then cured.
Stothers adds, “It is designed to quickly adapt and conform to the ideal shape during initial run-in of the engine and then stay on the piston for the remainder of service life. The adaptation is primarily due to the compression of the coating, rather than abrading. The coating is thicker than most coatings so it reduces the piston-to-wall clearance significantly, which is the goal.”
The advantages are more than just reduction in startup noise, though - Perfect Skirt reduces running friction, and perhaps most importantly, fights so-called “false knock” that can plague engines running the wide piston-to-bore clearance necessary for boosted powerplants. Unlike piston slap, which is mostly an NVH issue that doesn’t actually affect performance or durability, false knock can hamstring engines that rely on acoustic knock detection.
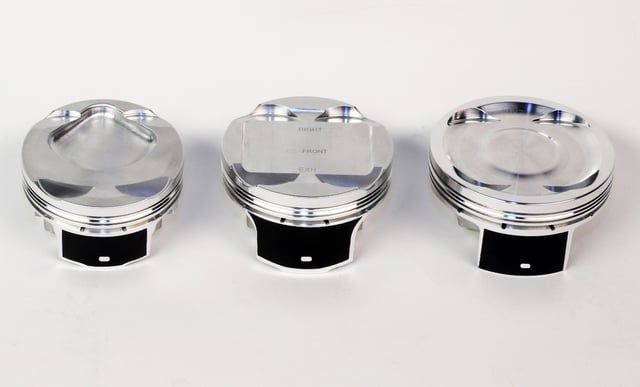
Inaudible to the human ear, the rocking of a wide-clearance piston in its bore can trigger the knock sensors in an engine that utilizes an ECU programmed to pull timing, boost, or both when detonation is detected. JE’s Perfect Skirt coating keeps pistons perfectly centered in their bores (hence the name) and prevents this potential performance-killer from ever becoming a tuning issue.
Because of the precision required for its application, Perfect Skirt is being introduced first in a select group of JE shelf stock piston designs for engines like the Gen IV LS and Gen V LT, VR38DETT, 2JZ-GTE, and 4.6/5.4/Coyote with the list continually expanding. Thanks to the unique properties of this coating, no bore undersize “fudge factor” will be required when sizing pistons with the Perfect Skirt treatment - if you have a 4.000-inch bore, order up a JE piston designed for a 4.000-inch bore and you’re good to go.
“The coating will help reduce noise but also stabilizes the piston, which is good for ring seal, wear, and general longevity of the piston,” Stothers concludes. Whether you’re just looking to quiet a startup rattle on your street build, or you want your boosted high-performance engine to have the advantages of a conformal dry lubricant treatment that dynamically reduces piston-to-bore clearances, JE’s Perfect Skirt is worth investigating.