For 2018, Ford redesigned the Coyote engine. It continues to make use of the traditional sequential port fuel injection found on every Mustang since 1986, and now has a high-pressure direct-injection system. This inclusion necessitated a number of changes to the piston design, and pushed JE to go back to the drawing board in its search to manufacture the ultimate Coyote piston.
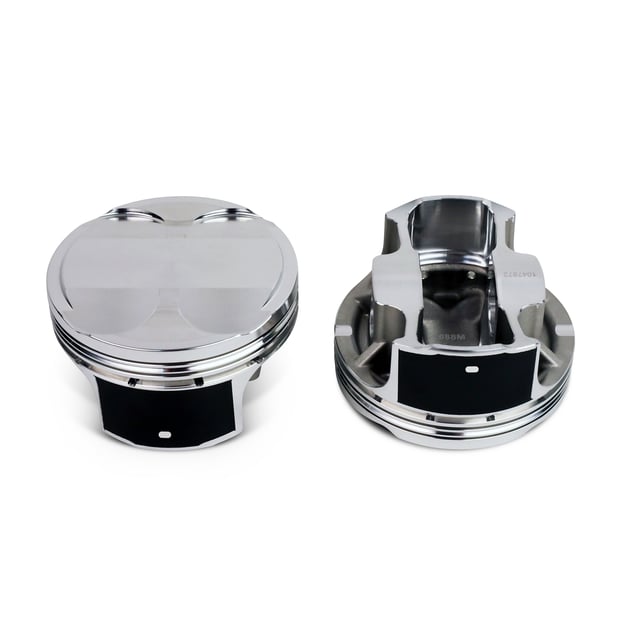
OE Design Element Changes & Additions
The 2018 Coyote engine produces 460 horsepower right out of the gate. Through the use of Ford's exclusive Plasma Transfer Wire Arc (PTWA) cylinder liner technology, previously found only in the GT500 and GT350 engines, the bore dimension of the Coyote was enlarged to 3.661-inch (93mm), up from the 3.630-inch (92mm) of the previous two generations of the engine platform. Stroke (3.650-inch), rod length (5.933-inch), and deck height (8.937-inch) remain the same. Compression is also pushed up to 12.0:1, up from the last generation's 11.0:1 ratio. Other engine changes include new camshafts, a new intake manifold, and the engine continues the use of the Charge Motion Control Valves as found in the Gen 2 engine.
“The Gen 3 Coyote is very different from the Gen 1 and 2 piston, which utilized the same piston design for both. The Gen 3 engine added direct injection which has enabled Ford to have even more precise fuel control. The crown shape of the pistons needed to be designed to accommodate the direct injection bowl and geometry,” says Nick DiBlasi, Director of Product Management at JE Pistons.
The new fueling strategy allow the compression to be raised to 12.0:1. The use of Ford's excellent Twin Independent Variable Camshaft Timing (Ti-VCT), through which a savvy tuner can independently advance or retard camshaft timing—for both intake and exhaust camshafts—to take advantage of the high factory compression ratio and direct injection, which really allows this engine platform to really make excellent power, especially when boost is added.
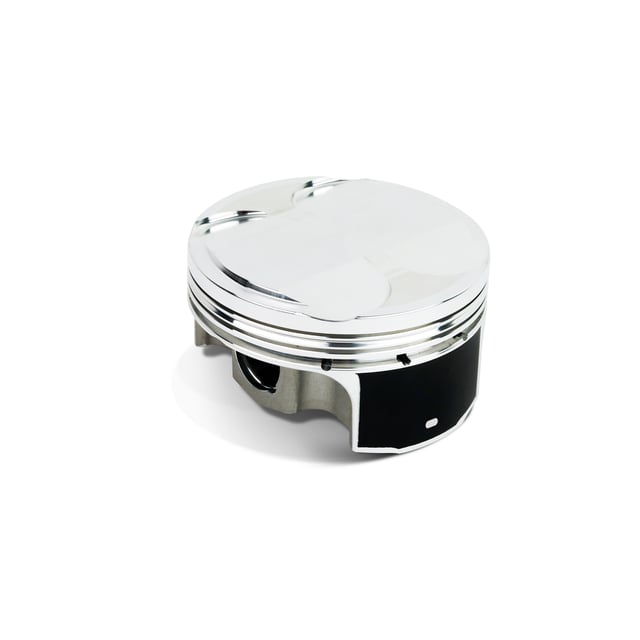
Performance Baked In
But these changes present challenges to the piston designer as well, since as an enthusiast adds boost and more power to the engine, eventually there comes a breaking point—literally—where the rotating assembly must be upgraded to support these elevated power levels. That's where JE's pistons enter the equation.
Learn More About JE Perfect Skirt HERE.
To best service the Coyote engine platform, JE has developed a dedicated forging that has been specifically designed for these engines and their high horsepower capabilities. It utilizes one of JE's Forged Side Relief forgings, which offers many benefits. Chief among them are the reduced skirt width and a shorter wrist pin, which reduce reciprocating weight without reducing strength.
The narrow skirt reduces piston contact to the cylinder wall to minimize friction, while the pin location is offset toward the major thrust side of the piston to help reduce piston noise, critical for those engines which are run on the street.
Taking advantage of the latest thin piston ring technology, these Gen 3 Coyote pistons use 1.0/1.2/2.8mm piston rings to reduce friction while maintaining ring seal.
Direct-Injection Considerations
The dual-fueling strategy (port and direct-injection) of the Gen 3 Coyote engine means that special attention must be paid during the design process to ensure that the piston's architecture is properly configured to provide proper performance in both situations.
“The crown shape of the pistons needed to be designed to accommodate the direct injection bowl and geometry. The direct injection bowl design is critical as we must ensure that the bowl shape and geometry matches the injector angle. If it is slightly off you can miss the bowl and fuel wash the back of the cylinder causing damage,” says DiBlasi.
“We maintain the shape as close as possible [to the OE design]. When adjusting compression ratio the total volume is affected, however we keep the diameter, depth, and location of the bowl in order to make sure the direct-injection functions as designed. We modify the remaining parts of the crown and valve pockets to compensate.”
The Perfect Skirt
One of the biggest—and most impressive—advancements in JE's recent piston design arsenal is its new Perfect Skirt coating, which is a patented process designed to reduce friction and wear.
Traditionally, forged pistons made from 2618 aluminum alloy have required piston-to-wall clearance from .003- 008-inch, sufficient to allow the piston to expand as it is faced with the heat of the combustion process. Perfect Skirt is a solid-film lubricant which is applied to the piston skirt with a patented, proprietary process; everything from the lubricant formula to the tooling and process required for consistent application was designed in-house at JE Pistons.
“The motivation was to develop a robust skirt coating that could be applied and bonded thicker and allow the forged piston to be installed at the same or less cold clearance than a cast piston, as measured on the coating,” says DiBlasi.
Using a three-stage bonding process, Perfect Skirt is permanently applied to the piston skirt and is designed to remain throughout the piston's life, not wear off as previous coating types have done. It is applied in a specific thickness which reduces the piston-to-wall clearance to levels typically seen by cast, original-equipment pistons which are designed for quiet operation over nearly all other considerations.
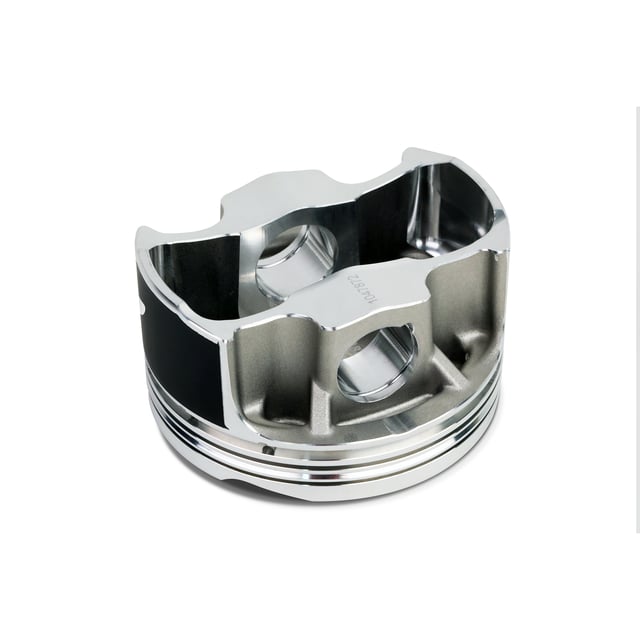
According to DiBlasi, Perfect Skirt has the ability to automatically fit itself to the specific bore in which it is installed; upon initial startup of the engine for the first time, Perfect Skirt quickly adjusts to this measurement and equalizes to the dimension of the bore.
The coating also provides an advantage with respect to use in modern engines such as the Gen 3 Coyote, which uses four sophisticated knock sensors as part of its engine management strategy that allows the 12.0:1 compression ratio to work properly with 93-octane pump fuel. By reducing engine noise, the Perfect Skirt coating drastically reduces the chance of false knock picked up by the sensors as the piston moves up and down the bore, which could easily occur with larger piston-to-wall clearances.
DiBlasi notes that pistons manufactured with Perfect Skirt will actually measure larger than the same piston with a bare skirt, and this is the intentionally-produced condition which is designed to reduce the clearance but not produce any adverse conditions during operation.
“The bore diameter of the engine should not be increased to account for the Perfect Skirt coating thickness. Oversizing the cylinder to accommodate the Perfect Skirt coating thickness will nullify the benefits of the Perfect Skirt coating technology. Special break-in procedures are not required with this coating,” says DiBlasi.There are four part numbers available: one each for forced induction or nitrous use in 93mm and 94mm bore sizes, for those racers who use sleeve the block or use an aftermarket block with the larger bore dimension to make a 314 cubic-inch Coyote.
Ultimately, JE has taken all of its latest advancements in piston design and coating technology, wrapped them up into one well-designed package, and created a Coyote piston which can withstand immense amount of power while running quietly and reducing internal friction. We'll call that a win-win for everyone.
For more information, give the JE team a call at 1-714-898-9763 or checkout the full catalog HERE.