JE Pistons has innovated a game-changing new way to forge pistons that aligns the metal grain of the aluminum material to add strength from the inside out. Read all about it here.
Forged pistons have been made the same way for decades, with differences in machining the primary means by which one supplier’s product can be differentiated from another. But now, a new development called Aligned Grain Flow Technology (AFT) provides a breakthrough, offering additional strength without additional mass.
After several years of experimentation and development by JE Pistons' Advanced Product Development group, AFT has been launched into the market in JE’s Ultra Series pistons.
- For all JE Ultra Series Domestic Applications, CLICK HERE
- For all JE Ultra Series Sport Compact Applications, CLICK HERE
AFT is about making the best use of the grains of metal within the piston. A forged piston is already stronger than a cast one. The cast piston has larger grains that are more three-dimensional in shape, but the source material for the forged piston – a long aluminum extrusion that’s cut off into piston-size slices – means that those grains have already been worked into a longer, thinner form, which helps to prevent crack propagation.
JE's idea was to make even better use of the inherent advantages of forging and optimize crack resistance in highly stressed areas, such as where the pin tower meets the crown.
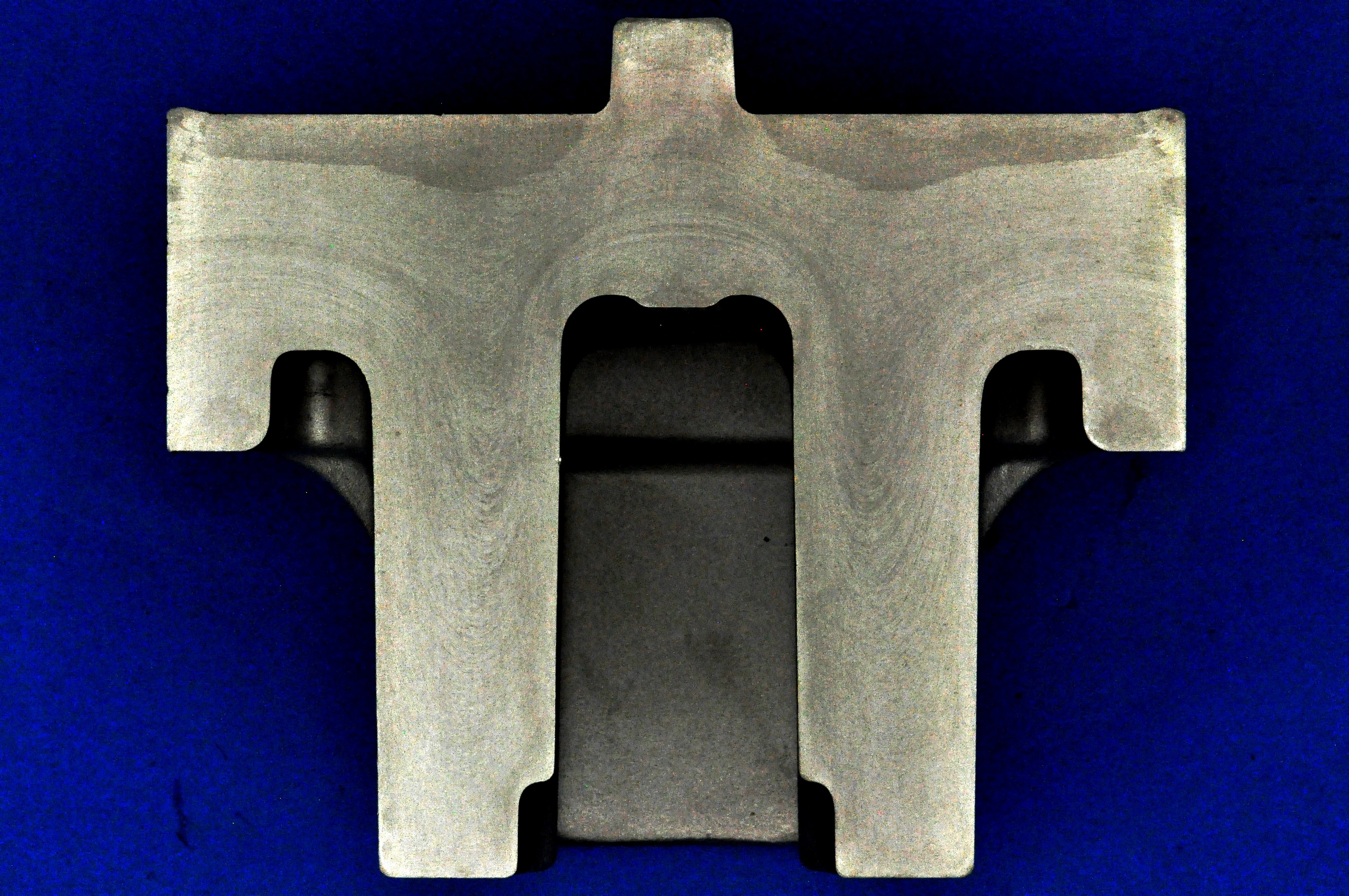
“There were additional manufacturing steps that we had to take to ensure that the grain structure was in the proper locations,” says Cody Mayer, JE Piston's Senior Manager of Advanced Product Development. “We further work those grains to stretch them and form them around the contours of the piston forging shape. Longer, thinner grains that are compressed more tightly together create additional grain boundaries in the most critical areas.”
In a piston, the grain boundaries in the metal provide resistance to cracks. Think of it as chopping a log: it’s much harder to cut across the grain, with each wood-cell fiber providing resistance to the axe. But if you slit the log from the top, it’ll crack much more easily along the grain.
“When a crack propagates through the material, it rarely happens all at once, especially in a fatigue situation in a reciprocating engine part that’s experiencing millions of load cycles,” says Mayer. “The crack starts very small and grows over thousands of cycles. But the elongated grains, packed tightly together, form walls to prevent the crack from progressing. The crack stops every time it hits a grain boundary. It’s much more difficult for it to propagate far enough through the piece to cause a failure.”
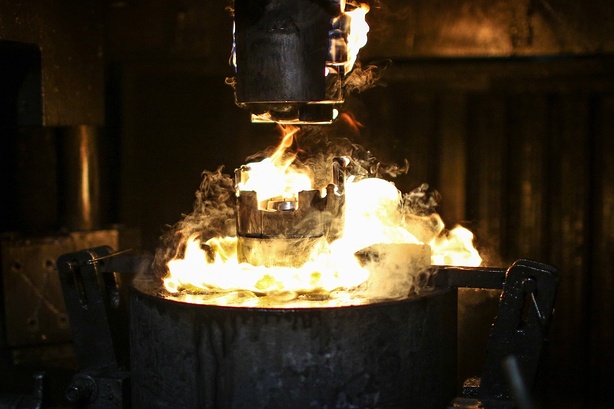
By placing the grain boundaries at the most highly stressed points on the piston, fatigue cracks can be resisted much more successfully.
“We’ve focused on the crown of the piston, in particular where the pin tower meets the crown,” he continues. “We’ve wrapped grains around that joint and extended them across the face of the crown to resist the bending that combustion would normally induce. We’ve also applied them to the skirt.”
A similar principle is already used in the manufacture of connecting rods, whose elongated shape lends itself more easily to exploiting the grain advantages of the source extrusion. It was no easy task to do the same thing for a piston, however. To begin with, JE Piston's engineers used software to simulate the grain flow during the forging process. Subsequently, physical test samples were sectioned and etched to check the grain alignment after each change to the process.
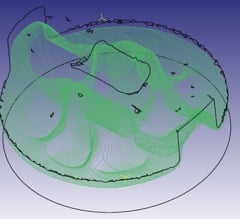
JE’s forging facility, just 100ft from Mayer’s desk at the manufacturing center in Mentor, Ohio, enabled the development team to quickly test the impact of new processes. New tooling was also required, but this too is made in-house, which further reduced the development time and ensured that every option could be explored on the road to the best result.
“If we had been working with an outside supplier, we probably would have not had the ability to fine-tune the process in the way that we did,” Mayer confirms.
That final process will remain a trade secret, but JE Pistons has a patent pending for Aligned Grain Flow Technology itself – the way in which it orients the grains and structures them for increased strength.
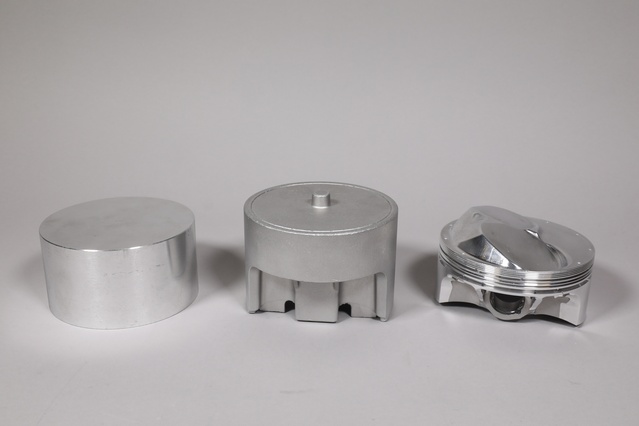
And while AFT is making its market debut on the premium Ultra Series pistons, which are available for a number of domestic and import engine families, the technology lends itself to many applications.
Ultra Series Applications
- Chevrolet LS and LT Dish, and Flat Top
- Ford Coyote Gen I-III
- Honda K Series and K20C
- Subaru EJ Series and FA20DIT
- Mitsubishi 4G63 and 4B11T
- Nissan SR20
- Toyota 2JZ
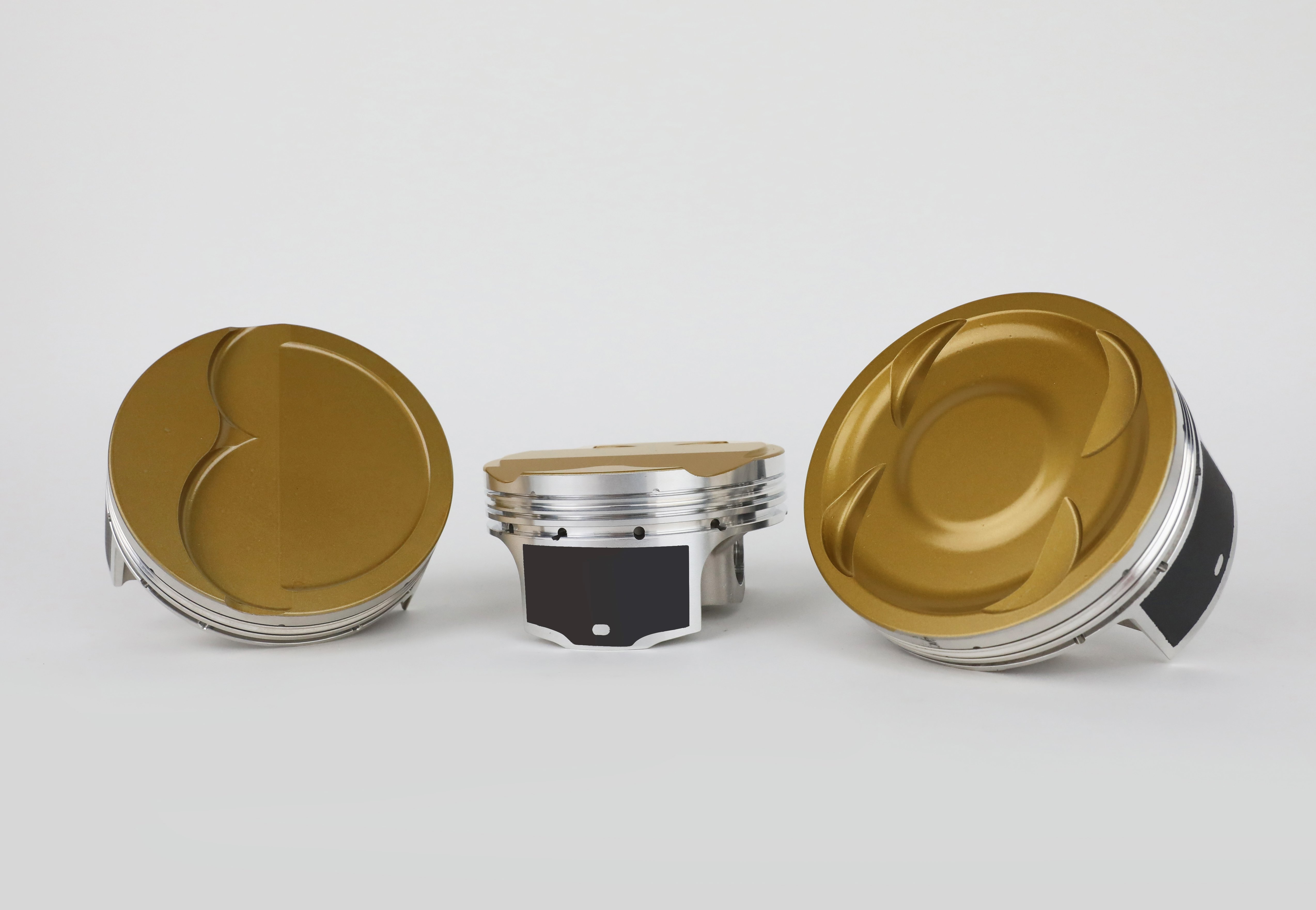
“AFT makes the piston stronger,” Mayer concludes. “We could have gone in two directions with that. We’ve chosen to start with Ultra Series pistons that are of equal weight but stronger, for high-power, high-boost applications. But the technology would apply equally well to taking weight out of a conventional forged piston, while maintaining equal strength.”