There's a lot that goes into piston design and one of those aspects is the skirt. The less drag created by the skirt on the bore equals more power. Check out how JE continues testing different skirt profiles for maximum power.
Working at the forefront of piston technology presents evolving challenges in designing piston skirt profiles with advanced cam shapes and barrel profiles to meet the escalating demands of the racing and high performance community. JE engineers continue to pursue innovative new ways to design and validate new piston designs. A characteristic example is their detailed development program for GMs popular LS series engines. Here’s why.
Designers have long understood that the most critical engineering aspect of advanced piston design incorporates carefully tailored skirt shapes and optimum ovality (cam shape) to suit every application. Clear evidence of JE’s attention to detail is seen in its unique line of asymmetrical pistons that incorporate different skirt panel widths for the major thrust side of the piston versus the minor thrust side.
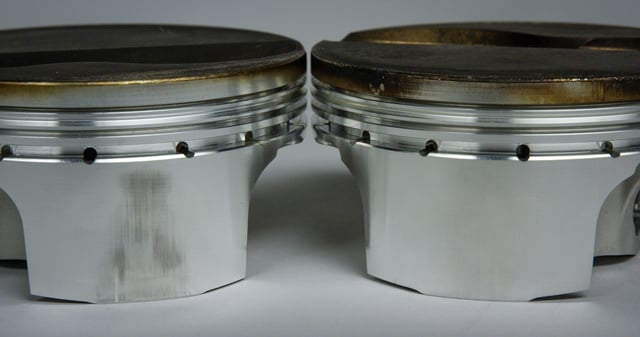
The advantages have led to lighter, stronger pistons with reduced friction properties. The development and application of individually tailored piston shapes and dimensions further impacts piston wear patterns, ring stability, noise levels and friction characteristics throughout the service life of the piston. The result of ongoing R&D programs that address these problems broadly reinforces JE’s manufacturing accuracy and quality control to ensure highly precise and matched pistons for any high-performance application.
The critical shape of the piston, its ovality and installation clearance are decisive factors affecting performance and long term satisfactory operation of the piston in the cylinder. Ring stability at the piston rockover point and subsequent pressure build is very critical and largely controlled by the piston skirt. Frictional forces on the skirt and the skirt lubrication characteristics are also critical for trouble-free operation. The gap or lubrication window between the skirt and the cylinder wall is established by the proper skirt profile, ovality and operating clearance. In this complex environment, the hydrodynamic lubrication toggles to mixed lubrication as the piston slows down approaching top and bottom dead center.
At the piston reversal points (top and bottom dead center) the mixed lubrication condition moves to a boundary lubrication condition. The piston’s skirt profile is tasked not only with distributing the thrust loading from combustion and maintaining optimum ring seal, but also maintaining the desired lubrication boundary to ensure good durability under high dynamic conditions.
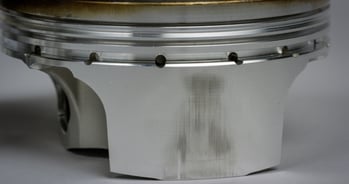
Developing skirt profiles and cam shapes to deal with the expansion characteristics of aluminum piston alloys remains a fundamental challenge to piston engineers. Pistons do not expand evenly, primarily due to uneven piston heating caused by combustion heat acting directly on the piston crown, and the non-uniform shape of the piston itself. The piston by necessity incorporates sections of varying thickness (heavy in the pin tower area, thinner in the skirt area) that require the skirt profile and cam shape be appropriately and accurately matched to the thermal and mechanical loading conditions. Exposure of the piston crown to high combustion heating requires more clearance in the adjacent land area of the piston to allow for the greater heat expansion than in the lower extremities of the skirt.
The classic “Barrel Shape” skirt profile remains the most common profile because it addresses many of the unique problems of piston design. But technology is a moving art form and there are still advances to be realized from this basic piston shape. In addition, the expansion of the area adjacent to the thicker section of the pin boss region also warrants attention. Machining the piston to an elliptical shape (smaller diameter near the pin bore area of the skirt than on the major and minor thrust areas) provides the ovality which helps to distribute thrust loading with minimal friction. For many years, this shape was achieved by mounting the piston on a rotating, clocked spindle that was moved in and out of a rotating grinding wheel via an eccentric cam device. Ovality in “cam ground” pistons is adjusted to suit the application and anticipated loading.
With a conventional cam-grinding machines, the ovality is applied to the piston at the same value for the full length of the skirt top to bottom. This means that the area of largest expansion requires the entire length of the skirt to be ovalized to meet its maximum expansion requirement. It allows the piston to expand and run without seizure in the cylinder, but results in a less than desirable loose fit of the remaining skirt area, which can contribute to inaccurate guidance of the piston in the bore and reduced ring stability.
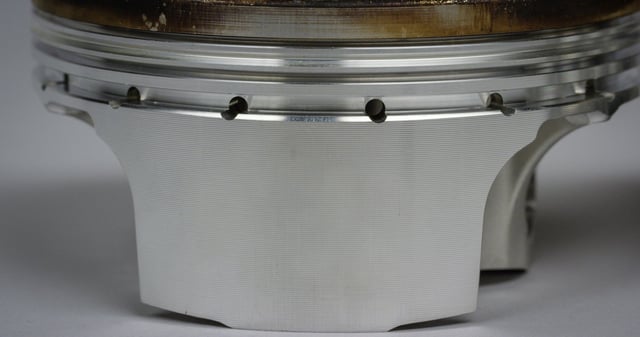
More modern diamond turning has replaced the older grinding method of finishing the O.D. to size, and variable camming of the skirt has allowed pistons to be designed with ovality to address the specific expansion characteristics of the entire piston skirt. to Compounding the complexity are other shape and ovality fine tuning strategies such as asymmetrical profiling of the major and minor thrust areas of the piston and reverse camming of certain areas of the piston.
Engine performance is significantly impacted by the friction force against the cylinder wall and piston rock over which can affect piston ring seal. The difficulty of determining the piston profile stems from the fact that piston primary and secondary motion and thermal deformation are not all that have to be taken into consideration. The piston contact area is also a function of actual cylinder bore geometry, which can be less than ideal at operating temperature. In addition, considerable skill is required in the development stage to critique piston and cylinder bore markings produced by the profile test in a running engine, and provide the proper corrective action.
These challenges can be successfully addressed with experience and advanced production methods. The skirt length and skirt contact area of a modern slipper skirt type piston are much reduced compared to earlier “full round” piston design. And unlike a full round piston, the land area is often designed to add guidance to the slipper skirt piston.
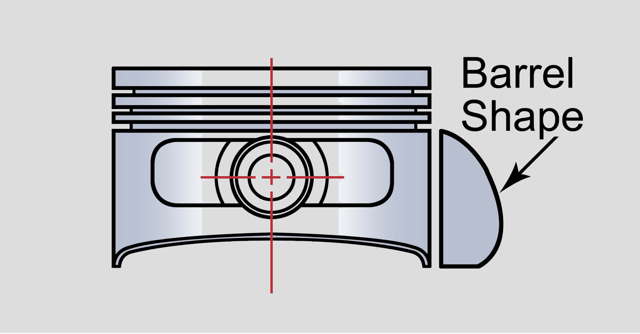
JE Pistons has dedicated considerable resources to the development of its performance products. Their in-house R&D Department operates three fully instrumented engine dynamometer cells at its Mentor, Ohio headquarters. As part of this ongoing development process, JE is devoting significant development time to further refining the shape and ovality of high-performance pistons for the broadly popular GM LS series engines. A new state-of-the-art dyno test cell with a new and fully instrumented Superflow SF-902 engine dynamometer is specifically dedicated to this project along with two new GM LS3 development engines.
A comprehensive array of engine performance inputs is systematically recorded and analyzed during the shape and ovality development testing with the LS engine. Among the measured and recorded inputs is real-time piston ring blow-by data measure via crankcase pressure instrumentation. The piston shape and ovality of the pistons for the LS3 test program are developed in house and produced on state-of-the-art equipment. JE uses its own in-house Variable Cam turning equipment and specialized software to create these precision piston skirt shapes.
The challenge early on was to create a software package to streamline the cumbersome programming of complex Variable Cam turned shapes. To support this program, JE’s engineering department developed a software package designed to address the complicated multi-dimensional geometry that characterizes automotive pistons. The process incorporates a Mahr gauge to measure and analyze precision piston features such as piston ovality and skirt taper.
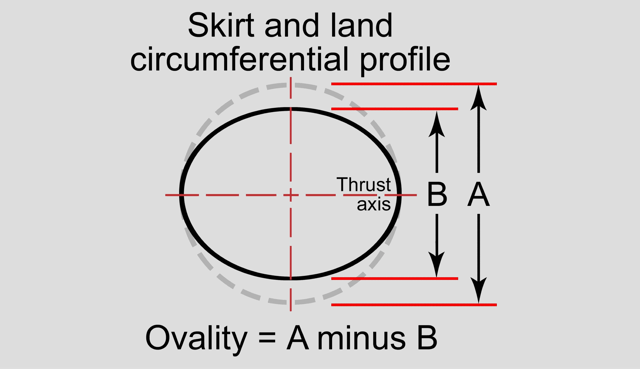
Automotive pistons incorporate difficult design geometries and odd dimensions because they are intentionally manufactured out-of-round and barrel-shaped below the ring lands. Typical geometric design software expects to see parts with traditional shapes that are either round, straight or angled. When you introduce an oval or complex barrel shape it responds with an error notation. JE had a need to carefully define these oval and barrel shapes with nominal specifications that could easily be repeated and accurately checked for conformance.
A Formscan circular geometry gage from Mahr Federal, Inc. enables the engineers to assign and measure a piston skirt’s change in radius at any angular point. The proprietary JE software allows them to assign alternate specifications for say, the angular offset for the high point or to specify specific skirt tolerances for the LS asymmetrical pistons that incorporate different shapes and sizes for each skirt. Their in-house software engineer accepted the difficult design challenge and produced the advanced software needed to accept input of the complex profile and ovality specifications and automatically produce code that is sent directly to the Variable Cam Turning machine. The proprietary software is named Auto Varicam.
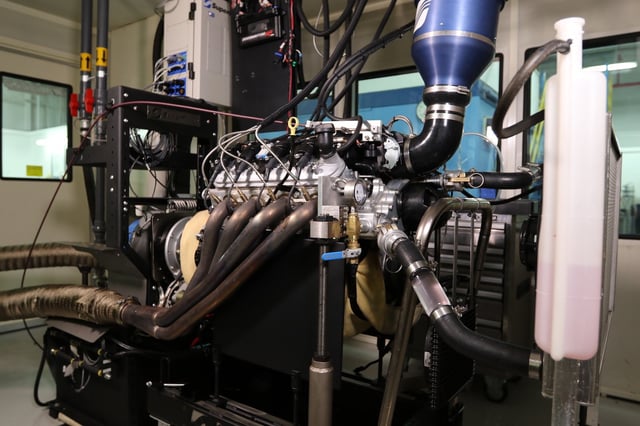
Test parts are machined and then measured on the Formscan gage and then analyzed with the design software to verify compliance with the design specs. It’s not a one stop process and often requires revisions based on the software analysis and dyno test results where piston performance is recorded and then physically evaluated for skirt performance via wear patterns and recorded data addressing blow-by, frictional torque characteristics and other factors. Based on analysis the CAD file or the CNC programming is fine-tuned to achieve the piston shape with the best performance characteristics. So, real world testing results are incorporated to compare the LS piston’s actual performance with the software’s predictions
This innovative approach significantly reduces the programming time and delivers a state-of-the- art variable cam shape development tool used by the Engineering and R&D department in the creation of very complex and accurate cam shapes. And the most compelling advantage of developing the Variable Cam Turning machine and the Auto Varicam software in house is that both key elements of this comprehensive system were developed by their own piston experts for the singular purpose of making the best pistons available anywhere.
When you purchase these pistons for your race car or high-performance vehicle, you’re buying more than just appropriately shaped slugs of aluminum with grooves for the piston rings. You’re cashing in on some of the most advance piston technology and quality money can buy. The load bearing and friction characteristics are second to none and you can be assured of optimum ring stability under the most severe dynamic conditions. So, whether you’re an engine builder or a one-off garage builder, you still get the best stuff and you can expect top quality and performance for the buck.