There's a lot more that goes into designing the crown of the piston. We discuss dish, dome, and flat top design considerations.
Automotive performance pistons are manufactured in flat-top, dome or dish configurations—but such a variety in crown design doesn’t suggest that engine builders will always have a choice.
“Piston crown design is driven solely on two things: your valve pocket requirements and your compression requirements,” explains Nick D’Agostino.
Crown design is drawing more attention from engine builders these days because that piston element is effectively the structural floor of the combustion chamber. Therefore, it contributes to all the dynamics involved in providing successful combustion, including air inlet airflow quality (swirl, tumble, etc.), flame travel and fuel distribution with direct injection (DI) and diesel engines.

“That’s really where everything happens,” stresses D’Agostino, who defines the piston crown as “everything that sees flame.”
Thanks to improvements in race fuels, cylinder head designs and sophisticated fuel-injection management, compression ratios have increased steadily in both factory and race engines (where rules allow). In older generation engines, higher compression required mountainous piston domes to fill up the large-chamber heads. Now, however, engine builders are leaning towards small combustion chambers with flat-top pistons—or at least pistons with restrained domes—to achieve a higher CR.
“Flat-top is the ideal scenario,” says D’Agostino. “It's going to be your best burn, most efficient as far as combustion efficiency is concerned. When we have to vary from that, we try and do it as subtly as possible.”
The perfect combustion chamber will always be debated, but one key consensus is that a centrally located spark plug is most efficient. That location minimizes the distance needed for flame travel to all points in the chamber, provides better flame front surface and usually requires less ignition advance to achieve complete combustion.
A center-mounted plug is easier to execute in a hemispherical chamber for a 2-valve cylinder head or a pentaroof chamber in a 4-valve head. More challenges, especially for piston designers, come with wedge and splayed-valve layouts that are popular V8 street and race engines. With that premise in mind, dome pistons often present the toughest challenges to piston designers.
“As you go on the power stroke, the flame front will be inhibited by a large dome,” says D’Agostino. “One of our steps with a dome piston is to radius it and keep it as low and broad as possible. Low, wide, broad domes are definitely more in favor than a tall peaky dome.”
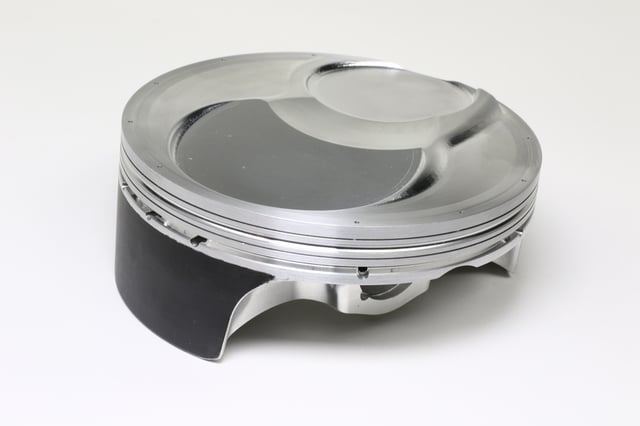
Combustion Chambers VS Piston Design
Such challenges are not limited to conventional big-block Chevy heads with open combustion chambers over 100cc. Some savvy racers are taking used, high-flowing NASCAR cylinder heads with small, high-burn-rate combustion chambers that were designed to work only with required 12:1 flat-top pistons and converting them to a high-compression Comp Eliminator or street-race setups.
“This happens all the time and we love it,” beams D’Agostino. “Take a Yates head or SB2.2 that comes out of a former Cup service where they ran a flat-top piston with a very small chamber, like 37 or 40 cc. Now this fellow wants 16:1. The biggest problem you run into is the valve pocket requirement. You create 12 cc's negative of valve pocket. Now you have to try to fit dome in places where there's just no real estate."
“You're trying to overcome valve pocket depth, but at 16:1, you need the big healthy camshaft that requires deep valve pockets. It becomes a battle of real estate at that point as we balance positive and negative to get to a number that makes sense for everybody,” adds D’Agostino.
Balancing positive and negative volumes are critical factors in designing piston crowns for high-compression engines that sport aggressive camshafts.
“As far as camshaft and valve pocket requirements, the valve-pocket sizes and depths, of course, create a negative. One of the things we talk about a lot is effective volume,” explains D’Agostino. “People say they have a crown volume or a dish volume. We look at it as a total effective volume because the valve pockets also create a negative. We'll actually have some pistons that have a dome on them, but still have a negative effective volume. They might have a 4cc positive dome, but they have a 10cc negative valve pocket. It's still a 6cc negative effective volume, even though it has the shape of a dome piston.”
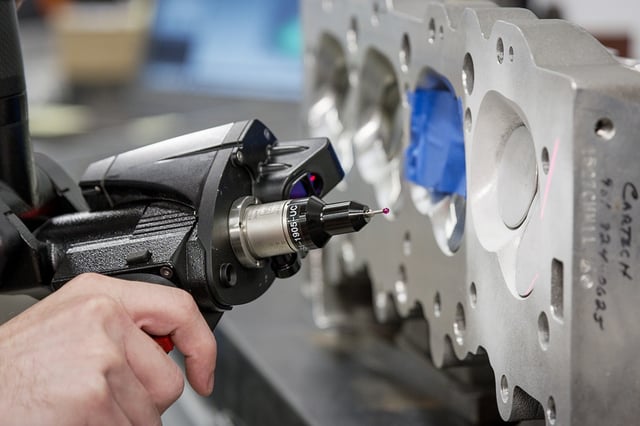
Add nitrous to these small-chamber heads, and it could get ugly in a hurry.
“We'll see some folks that are using nitrous or something like that in those smaller chambers, and they burn pistons constantly because the margin of error in the tune-up is very small. The more compression you put into that chamber, the quicker everything is going to burn,” says D’Agostino.
Even with large-chamber heads, understanding the dynamics of spark control and flame travel is critical with pistons where piston-dome volume approaches 50cc.
“One of the things we look at with our dome pistons is dome height. We'll get to a point of diminishing returns where I might be able to take you from 14:1 to 15:1, but I'm going to create such a mountain for that flame and fuel to come over, that it's not worth it,” says D’Agostino. “More cases than not we'll have to reach back to the customer and say okay, this is a better design at 14 than 15.”
Once the correct valve-pocket depth is achieved, piston engineers can employ unique design elements to improve airflow into the cylinder.
“As far as unshrouding the valves in the pocket, we can open up the diametric clearance in the pocket to allow some breathing room. If we're after high compression, that real estate around the valve becomes very critical,” says D’Agostino. “We need to draw that in and keep a close radius and close diametric clearance. Similar to building a stocker, I've got to stay with the flat-top. But I want to run as big a valve as I can. I need to run a tight pocket clearance and minimal valve-pocket depth so that I can maximize the compression.”
Top Ring Placement
Valve-pocket depth can affect other piston design elements, even placement of the top ring groove. One of the most effective piston tricks is to place the top compression ring closer to the crown of the piston. With the right engineering, engine builders have seen up to a half-point more compression—which is very useful in high-competitive naturally aspirated applications like Stock Eliminator.
“Top ring placement is all a function of the valve pocket requirement,” says D’Agostino. “Imagine two lines, one representing the valve plane and the other representing the top ring groove, eventually those two will meet if they both keep going. Those lines will intersect.”
Some racers are asking to place the top compression ring groove only .100- to .120-inch down from the piston crown without fear of reliability issues.
“You have it up high, but you have a very narrow radial-width ring,” adds D’Agostino. “As you narrow that groove you pull it away from the valve pocket and you create material thickness there. That's one of the tricks that guys do to get compression.”
Another piston trick on high-strung motors is to mimic the valve-head profile on the combustion side. Some intake valves have rather profound dishes machined on the valve head to reduce valve weight, but that trick also opens up the combustion chamber and reduces CR.
“We can place the center point of the valve and with our inspection equipment pick up the feature of the tulip,” says D’Agostino. “Then we place that in the valve pocket so we can get a couple cc's back.”
Quench
The topic of quench is likely to arise during any discussion of piston crown design. It’s not as critical with boosted engines where engine builders are satisfied with .080- to .100-inch quench, but naturally aspirated engines continue to pursue every possible avenue of power production and seek .030- to .035-inch quench.
“It seems if it's forced induction, quench all but goes out the window. Again, I think you could talk to a lot of different engine minds and get some different theories there. Is it the most efficient opportunity and the best power making opportunity? Not always,” says D’Agostino. “With the power adder stuff, even a street car with a turbo, it becomes more about survival than power situations, like Engine Masters where we're working for max VE at all times.
“In applications where you're compression limited and you have to run a flat-top is where I see it most exploited,” adds D’Agostino. “When you get into dome situations everything becomes test fits and chamber molds. You're looking at the radius on the back of the dome. Is it clearing the chamber with piston rock? Is it going to hit? Are you going to clip a valve? Now you're getting into deep engine building because that's fitting every part to be specific.”
Gasket thickness can change the equation when designing a piston for valve clearance and quench.
“If it’s a small chamber, small-block, I'm limited on what I can do. And then he wants to run a .035-inch head gasket. Now I need to give you more valve pocket because you're going to collide and that's where we start going back and forth with the customer,” explains D’Agostino. “Okay, you're also at .035-inch quench, and the piston's at zero deck. Oh, you’re going to put in an aluminum rod, which has a tendency to stretch at temperature going through its cycles. I now have to drop the piston in the hole .010-inch. There went a bunch of compression, so you play it back and forth.”
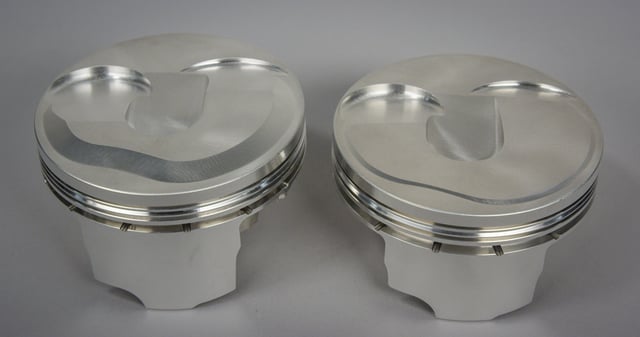
Direct Injection Considerations
Piston crown design can get more sophisticated when dealing with DI engines, but those piston manufacturers already involved with sport compact and diesel have an early advantage. Many of these projects involve increasing compression on factory engines, but D’Agostino cautions that the stock fuel system may not support such a move. The piston designer’s priorities, however, will still start with clearing the valves, then dealing with fuel requirements before addressing compression gains.
“Crown design becomes very critical as far as specific troughs. Use the LT for example, it has a specific trough there that is key to idling, initial startup (OMIT and things like that). That isn't so much a power consideration, but it's critical from an emissions standpoint,” says D’Agostino. “The OEs do hundreds of hours of R&D, so we work off of an OE sample and pick up those locations. As far as affecting spray patterns, the injector location remains constant. Piston crown coming from the bottom isn't going to affect the spray pattern or the cone angle. That's all a function of what's above. All we can really affect is that we're creating the combustion event in the proper spot on the piston.”
Dish Pistons
Dish pistons present the fewest problems for engineers because they’re mostly used in boosted applications which often don’t require high-lift camshafts or high compression ratios. But there is a science to designing the crown, and one of the first choices is the shape of the recessed area. One train of thought is that it should be an exact mirror image of the combustion chamber, which is called inverted dome. The other choice is a symmetrical dish with a consistent profile, or possibly a traditional D-shaped dish with a radiused edge.
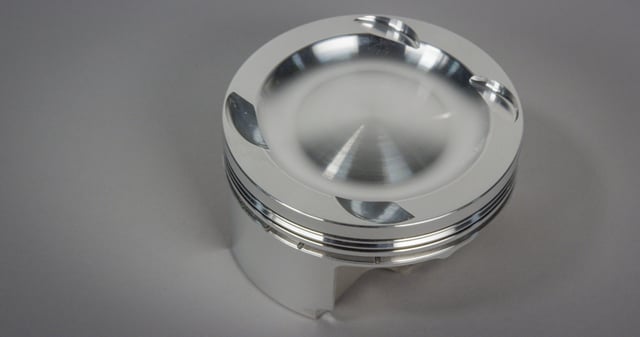
“Good luck getting common agreement on this,” quips D’Agostino. “As an example of an engine that was going to be detonation-prone, say a pump gas Chevy LS with a turbo on it, and it was going to see some street duty, I would go towards a spherical dish on that instead of a mirror image or a reverse dome to offer a softer dish feature and more flow to aid in a more efficient burn. I don't want the flame front, I don't want the fuel to have any opportunity to puddle. I would put soft edges on it and make the transition very gradual.”
When it comes to piston crown design, the demands of the different applications will dictate the choice as engineers address cam lift and compression ratio as well as other factors covering fuel and ignition. In addition, they still have to ensure durability while saving weight when possible.
“We’ll try to keep it as close to a flat-top design as possible,” sums up D’Agostino.