Naturally aspirated and power-adder engines produce hp in very different ways. Piston design has evolved tremendously to keep pace. Here we explain the differences between both types of pistons.
Previously Featured in Fastest Street Car Magazine.
Just like two camshafts that look similar can serve vastly different needs, the same concept applies to pistons. Many racers presume that a power adder piston is nothing more than a beefier version of a naturally aspirated piston. While there is some truth to this casual assessment, digging deeper reveals a multitude of key differences that impacts everything from durability to weight to stability to ring seal to power production.
Designing a power adder piston isn’t as simple as adding some extra metal here and there, then calling it a day. Reducing mass isn’t the only priority when designing a naturally aspirated piston, either. Since naturally aspirated engines and power adder operate at vastly different levels of cylinder pressure, heat and rpm, optimizing a piston for maximum durability and horsepower output requires an equally different approach to overall design.
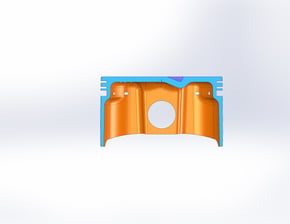
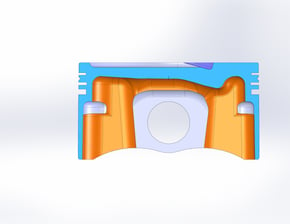
Challenging Forces
Fully appreciating the importance of tailoring piston design for an engine’s intended use requires examining the dynamic forces at hand in a high-output engine. During the power stroke, heat and cylinder pressure attempt to squish the top of the piston into the bottom of the skirt. At the same time, the piston skirts are pushed into the major and minor thrust surfaces of the cylinder walls.
Furthermore, as cylinder pressure attempts to blow the piston out the bottom of the block, the connecting rod and crankshaft resist this motion by exerting force in the opposite direction. It’s like firing a bullet, catching it with a cleaning rod, then pushing it back toward the chamber once it reaches the end of the barrel. The abuse doesn’t stop there.
After the piston returns to TDC, the rod and wristpin attempt to stretch it apart by exerting downward force during the intake stroke. Consequently, each and every section of the piston—including the crown, skirts, ring lands, wristpin, pin bores, and support struts—endure tremendous loads throughout the four-stroke cycle.
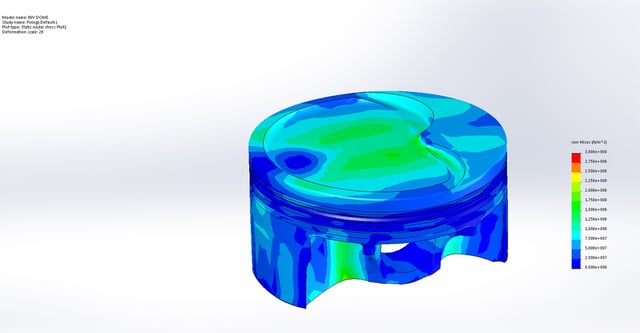
Material and Thickness
As an engine’s horsepower output increases, cylinder pressure and heat increase as well. While 4032 aluminum alloys work great in street/strip applications, the enhanced durability of 2618 alloys are preferred in both naturally aspirated and power adder-equipped race engines. Beyond sharing a similar metallurgy, however, naturally aspirated pistons and power adder pistons have very little in common.
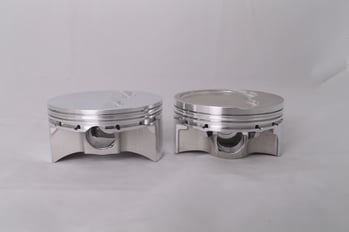
Granted that today’s crop of highly efficient naturally aspirated engines can easily exceed two horsepower per cubic inch, power adder combos can triple that figure. Consequently, they utilize thicker crowns, skirts, ring lands, struts, and wristpins. To account for increased thermal expansion, skirt and ring land clearances are increased as well. “Even a great piston material has a finite level of strength, and we must tailor the design to work within these strength limits. We do this by increasing thickness in key areas, adjusting clearances, and modifying the design to accommodate the specific application,” Clayton Stothers of JE Pistons explains.
Nevertheless, horsepower output isn’t always the best way to gauge piston load. “The amount of power an engine makes is only a piece of the puzzle. We must also take into account the application and duty cycle that a piston will see,” Stothers continues. “A 5,000hp drag racing engine may see less abuse than a 1,000hp offshore boat motor, simply because of the vastly different duty cycles. Naturally aspirated pistons can be made thinner and lighter while still maintain an appropriate level of stiffness and strength because the amount of stress they see is much lower.”
High RPM and Friction
Without the luxury of boost or nitrous to increase cylinder pressure, naturally aspirated race engines rely on rpm instead. Even so, the rigors of high-rpm operation still place substantial loads on the pistons. “A high-rpm naturally aspirated engine is similar to a power adder engine in the sense that the loads on the piston are increased. However, the difference is how that load is exerted on the piston,” Clayton Stothers explains. “In a high-rpm application, the goal is making sure that the pin bore area is strong and durable to prevent the pin from being pulled out of the bottom of the piston.”
Since frictional power loss increases dramatically at high rpm, pistons designed specifically for max-effort naturally aspirated engines utilize unique skirt shapes and profiles that reduce friction without compromising stability. According to JE, a stable piston than improves ring seal while reducing friction can be worth 10-20 horsepower over a standard piston. Traditionally, piston manufacturers have optimized the profile and taper of the skirts and ring lands to minimize the surface area of the piston that comes into contact with the cylinder walls. The idea is to have just enough skirt-to-cylinder contact to stabilize the piston, which reduces surface area and friction.
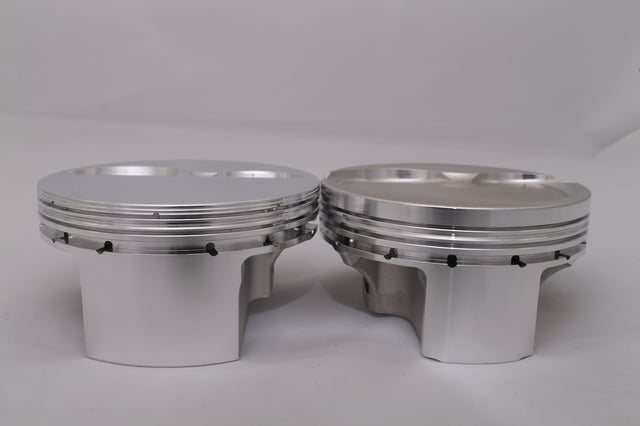
Asymmetrical Skirts
While optimizing skirt taper is still an effective method of reducing friction, JE has taken things to the next level with its forged side relief pistons. Unlike conventional full-round pistons, JE’s FSR pistons feature asymmetrical skirts that are very large and robust on one side, and much smaller and lighter on the other side. “The major and minor thrust surfaces vary dramatically in all engines. JE developed asymmetrical forgings so that these differences can be optimized,” Stothers adds.
As a result, asymmetrical pistons still provide all of the advantages that high-end naturally aspirated pistons have traditionally offered, but with further weight savings. “Our asymmetrical LS pistons, for example, are designed to handle large horsepower loads while still maintaining low weight by minimizing the skirt panel on the minor thrust side. Likewise, our lightweight FSR big-block Chevy pistons take a very large domed design and make it as light as possible. JE offers asymmetrical pistons for both naturally aspirated and power adder applications.”
Crown Design
In the past, naturally aspirated and nitrous pistons were easily identified by flat-top or domed crowns. Forced induction pistons could easily be spotted by their dished crowns as well. As modern cylinder heads have adopted smaller combustion chambers, however, it's not uncommon to run a dished piston in a naturally aspirated engine. Likewise, flat-top pistons are sometimes used in conjunction with copious deck clearance in order to reduce static compression in forced induction combinations.
Regardless of how the top of the piston is shaped, manufacturers can optimize the cross-section and underside of the crown for either naturally aspirated or power adder duty. “We take a close look at the thickness between the valve relief and top ring groove to make sure there is sufficient material in that area,” Stothers explains. “In addition to increasing the thickness of the crown to accommodate increased loads in power adder applications, we also use larger-radius contours on the bottom of the crown to decrease stress concentrations. The design and contour of the piston’s underside determines how evenly the top of the crown distributes heat.”
Pins and Bosses
For most racers, wrist pins are merely a necessary evil that add to the piston’s overall weight. In reality, reducing mass isn’t nearly as important as resisting flex, since the wrist pins are responsible for transferring the cylinder pressure exerted on the pistons to the connecting rods. As the pistons transition from TDC toward BDC, the pins prevent them from crashing into the cylinder heads as well. Wristpins that flex due to inadequate wall thickness can place additional stress on the piston. Similarly, reducing pin diameter in an effort to reduce mass concentrates a greater load over a smaller surface area in the pin bore and connecting rod, which can lead to cracking or galling.
While wristpin diameter is usually determined by the small-end diameter of the connecting rod, piston manufacturers often increase wall thickness as power levels increase. Higher-grade alloys can be used as well. Moreover, pin boss design also plays an important role in durability. “Typically, we will seek more engagement between the pin and pin boss towers to support the larger forces seen in power adder combinations. This can be done with either a longer pin or a narrower pin boss span,” says Stothers.
Rings
Although naturally aspirated and power adder pistons are subjected to different levels of heat and pressure, both have benefitted equally from the significant improvements in ring technology over the last decade. “Most performance rings consist of a steel top ring and a ductile second ring. Phasing out cast rings has significantly increased durability while allowing for a reduction in axial height,” Stothers explains. “A steel gas-nitrided top ring has proven to be the best combination for power adder and naturally aspirated engines. When combined with a hooked ductile second ring, this arrangement allows for better oil control, lower ring tension, reduced friction, and improved conformability and ring seal.”
Turbo vs. Blower vs. Nitrous
Granted that power adder pistons are more structurally robust than their naturally aspirated counterparts, but how are turbo, blower, and nitrous pistons different from each other? “Typically, we treat turbo and supercharger applications in a similar fashion, but with the cooling effect of nitrous, the piston design can be slightly lighter than a full-race forced induction part,” Stothers remarks. While effectively managing heat is critical in all power adder applications, it is particularly important with turbochargers. “We recommend ceramic thermal crown coatings in heavy-duty power adder applications. Coatings reduce the amount of heat that is absorbed into the crown of the piston, thus extending longevity. We have also see great benefits in turbocharged applications, where the crown coatings reflect most of the heat back into the combustion chamber and out of the exhaust, This helps maintain higher exhaust velocity for quicker turbo spool-up.”