By digitizing the chamber and using that as a map to create the piston top combustion surface, this mapping indicates potential problem areas that need to be addressed.
Previously Featured on EngineLabs.com.
In 1811, the Industrial Revolution was exploding across most of the civilized world. But not everybody considered these changes good. A small band of malcontents called Luddites, attempted to stop the industrialization of the textile world that was replacing their specialized weavers’ jobs with machines. The Luddites thought by smashing the machines and living in the past, their jobs would be safe.
Thankfully, the Luddites didn’t win that little insurrection and society and technology flourished. So while the Luddites have passed into history, so has the time-consuming procedure of hand-fitting piston tops to the combustion chamber, now yielding to digitized mapping of the combustion chamber. In this 21st Century world, builders now start by completing the combustion chambers, then JE Pistons offers a service that uses 3D scanners to create a detailed digital map of the complex chamber shape.
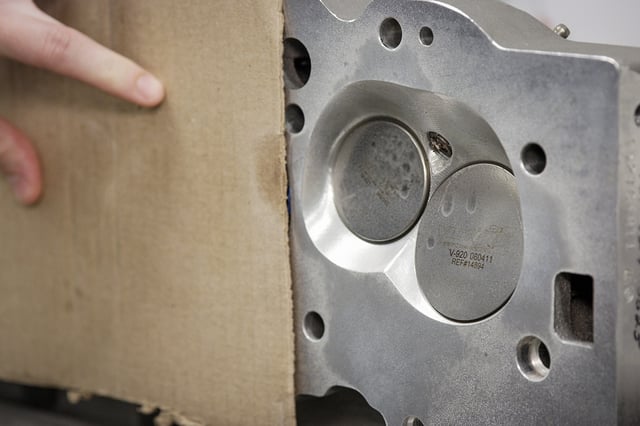
This scan is then used to direct the shape of the piston top to create the desired compression ratio while minimizing obstructions to the combustion process. Compression for big-bore long-stroke engines is easy, but it can sometimes be a challenge for short-stroke engines. Besides a small chamber, it’s often necessary to create piston domes to displace volume in the chamber. In extreme cases, large domes can reduce combustion efficiency – something that should be avoided.
By digitizing the chamber and using that as a map to create the piston top combustion surface, this mapping indicates potential problem areas that need to be addressed such as the narrow peninsula between the intake and exhaust valve pockets where the piston might strike the head.
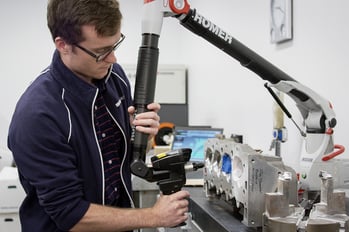

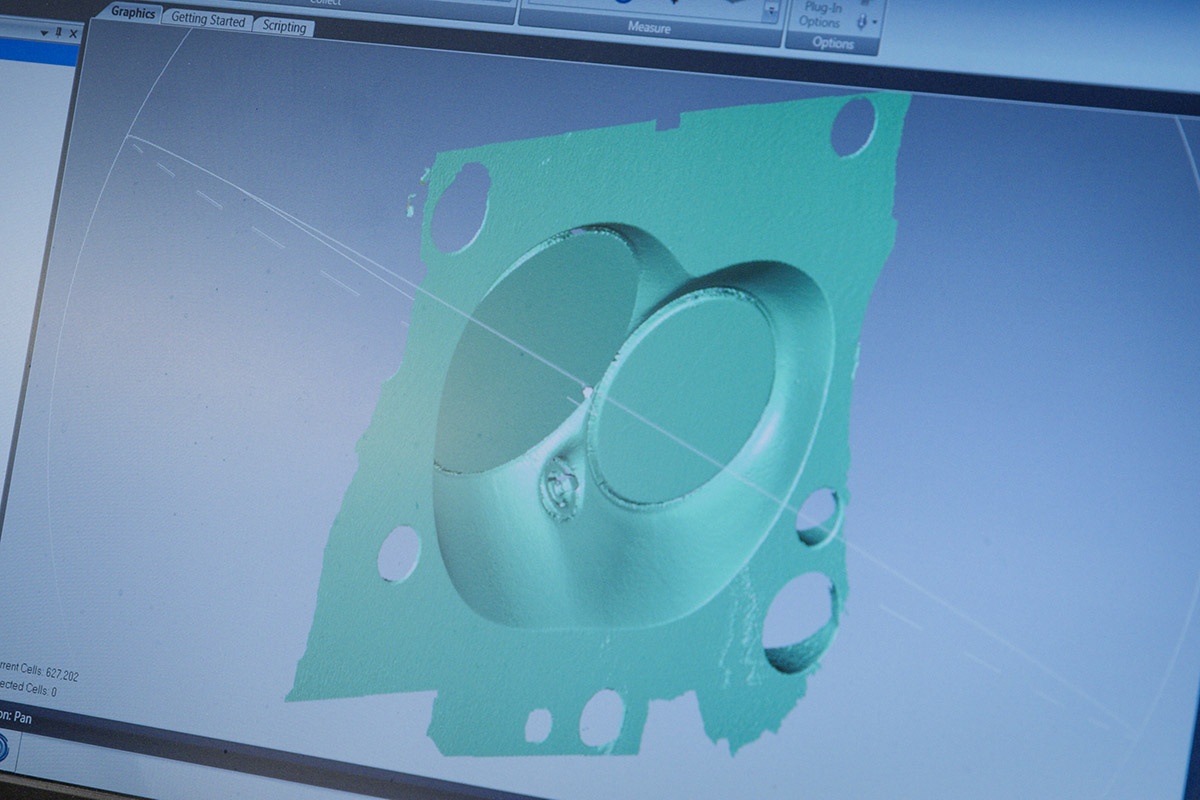
A good engine builder knows that block machining inconsistencies are an everyday fact of life that effect the process of custom fitting pistons to the chamber. Piston-to-head clearance is one of the most important variables that must be accurately measured and minimized. This dimension can be affected by a number of associated variables like a non-square block deck height, inconsistent rod length, or slight variations in the crank stroke. Even if a piston has been carefully digitized, any of the above variables will affect piston-to-head clearance.
Piston rock is another variable worth noting that must also be accommodated, especially if minimal piston-to-head clearances are anticipated. JE 2618 pistons generally run a relatively tight piston-to-wall clearance that helps maintain this integrity.
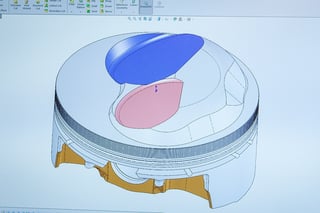
Another major advantage to the piston top digitalization is that the piston will arrive fully machined with smooth radius domes and radiused valve reliefs that will all but eliminate the tedious hours of gentle hand work that must be applied to the piston. Most engine builders will still want to put their final touches on new pistons, but the digital process offers a dramatically superior and more consistent piston top approach over the old school ways of hand-shaping piston tops. This allows the engine builder to spend more time on other areas where additional power can be squeezed out of his latest attempt at combustion wizardry.