JE Pistons is here to support your horsepower goals with our custom piston options; check out what's standard equipment and what's possible to take your performance to the next level.
With nearly 70 years of piston manufacturing experience, the team at JE Pistons knows what it takes to develop custom pistons to extract maximum horsepower and durability for your racing application. When it comes to a set of JE's custom pistons, the option list is nearly endless. The experts at JE will help you to determine which features will benefit your engine program and help to achieve your performance goals.
Every JE custom piston has these options as standard equipment:
- Full CNC machining
- Precision CNC machined ring grooves
- 2618 low silicon or 4032 high silicon material available on some applications
- Diamond turned skirts
- Single forced pin oilers or broaches
- Pick lock grooves for use with wire locks or carbon steel spiro locks
- Machined side reliefs on full round forgings
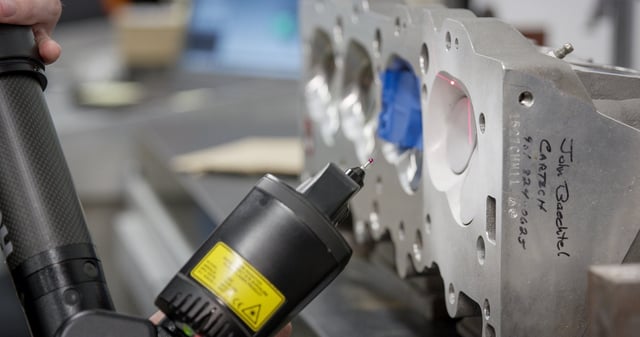
Custom Piston Optional Features
Ultra Crown Dome/Ultra Crown Inverted Dome
Mapping the exact shape of the cylinder head allows JE to create precise tolerances between the piston dome and the cylinder head. The Ultra Crown machining process permits optimum compression and quench characteristics to ensure a complete burn of the air/fuel mixture. This helps to reduce detonation as well.
3D Under Crown Milling
Reducing piston weight in areas where it's not required for strength will promote RPM capability from your engine. JE's 3D Under Crown Milling process removes this unnecessary material, which creates a uniform piston deck thickness and promotes piston durability.
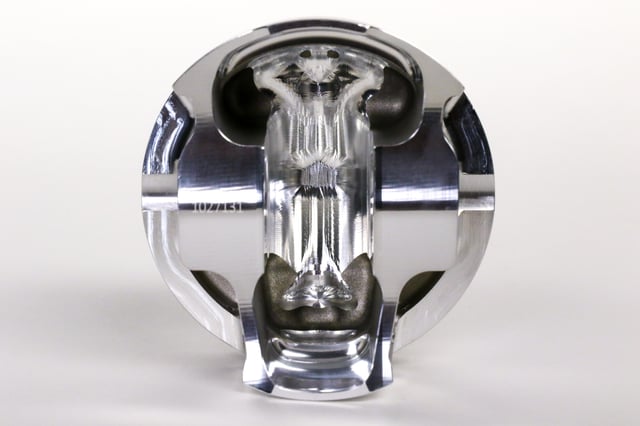
Vertical Gas Ports
Improved ring seal through piston design is the realm of vertical gas ports, which are small holes drilled in the deck of the piston and assist greatly in promoting positive ring seal. The holes are positioned to allow combustion gases to enter the ring land area on the power stroke to pressurize the area and push the ring out toward the cylinder wall. If the piston is not on the power stroke, the ring has normal tension to reduce friction. This option is most often used in drag racing applications.
Lateral Gas Ports
Lateral gas ports are small slots that are machined into the top of the top ring land and permit combustion pressure to enter the ring land area and get behind the ring. Most commonly used in circle track applications, lateral gas ports permit the use of a thinner ring pack and less ring tension, which works to free up power. Gas ports are an efficient way to force the ring face against the cylinder wall.
Ultra Groove
One of the keys to ring seal is ring groove flatness – the flatter the ring can be held during the combustion cycle, the better the ring seal will be, and this is where the Ultra Groove comes in. It's a special ring groove machining process that's designed to provide the necessary flatness, and a near perfect surface finish. Tolerances are held to millionths of an inch for accuracy.
Spin Boss, Window Milling, Plunge Boss, and Chamfer Pin Boss
These operations are designed to remove weight from the piston where it's not required for strength. Window milling removes material from the back side of the piston skirt, often a significant amount of weight, while retaining the strength of the piston. Spin Boss machining occurs on the bottom of the pin boss, where the extra material is not needed for strength. Chamfering the pin boss occurs on the bottom corners of the piston pin towers, and the plunge boss operation is completed at the base of the pin tower. Each of these operations is computer-modeled during the piston design process.
Contact Reduction Grooves
As the piston runs through the combustion cycle, it rocks slightly from side to side. Contact reduction grooves are machined into the the area between the piston crown and the top side of the top ring land. They help to reduce the contact area against the cylinder wall during piston rock. They also provide the added benefit of disrupting the flame travel into the crevice area, which helps to reduce the potential for detonation.
Accumulator Grooves
Ring flutter is a condition which occurs when combustion gases build up between the top and second piston rings; the Accumulator Groove is designed to reduce this pressure. It's machined into the land between the two rings and provides additional volume where the combustion gases can collect to reduce the chance of flutter. In the process, it also helps to promote top ring seal.
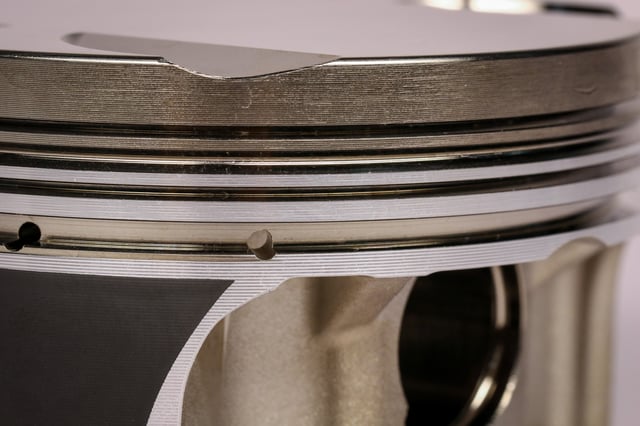
Double Pin Oilers
As you might guess from their name, double pin oilers provide the piston pin with twice the oil than the standard single pin oil system does.
Pin Fitting
Selecting the pin fitting option when ordering your custom pistons means that the pin bore will be precision honed to ensure an exact pin clearance for your particular application.
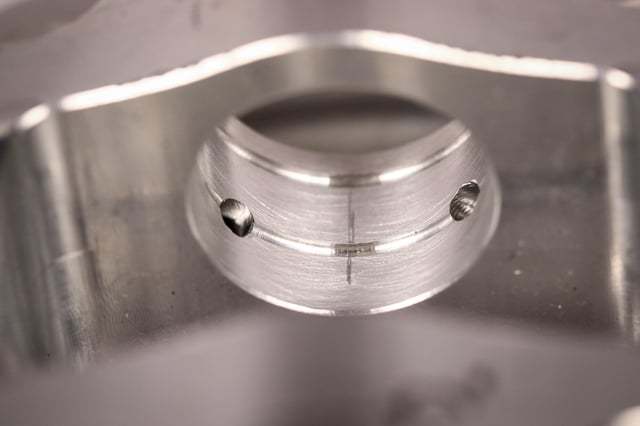
Oil Squirt Notch
Some late-model engines, like the 5.0-liter Ford Coyote engine and GM LS, have variants where piston oil squirters are installed. Oil squirters can also be installed with various aftermarket kits; These squirters are designed to cool the underside of the piston with engine oil; some pistons require special notches to be machined into the skirt. The notch process can be done for these application, or to avoid contact between pistons and/or pistons and crankshaft.
Bottom Oilers
For applications where high RPM and/or severe duty is encountered often, JE offers the option to have one or two bottom oil holes drilled into the bottom of the pin boss to aid in splash pin lubrication. Combine these with the double pin oilers to ensure maximum lubrication for the piston pins.
Tulip Valve Pockets
If achieving maximum compression for your Hemi or motorcycle engine is a major concern, select the option for Tulip Valve Pockets. This process leaves a raised area on plunged valve pockets to ensure you're attaining maximum compression with your build.
In Conclusion
There are many available options to choose from, whether you're selecting a shelf-stock piston part number applying one or more of the simple engineering changes, or developing a true custom piston for your application. JE's sales team and well-versed engineering staff can help you to select the appropriate options for your pistons to ensure success from your engine build.