We take a look at the difference between forged and cast pistons, and why forged parts are stronger and more reliable.
Strong and reliable engine parts can make more of a difference than some of us realize for racers, riders, drivers, and mechanics alike. Speaking from personal experience as a dirt bike rider and racer, I suffered a significant crash in 1991, when my motorcycle piston failed on the face of a triple jump, forcing me over the handlebars, resulting in two broken arms, four surgeries, and the end of my professional racing dream. After this eye-opening experience, I began to educate myself on the origin of parts used in my bike. I began with the differences between forged and cast metal processes, including their benefits and drawbacks. Regardless of the reasons behind the parts we choose, we should all know a little more about their development before throwing a leg over a motorcycle or getting behind the wheel of a race car.
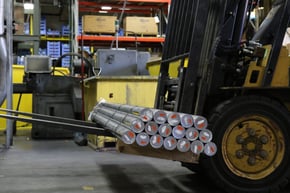
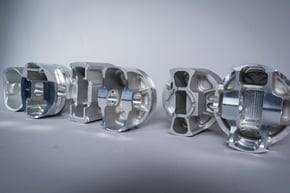
Most of us have heard the terms “casting” and “forging” in relation to the foundation of pistons and engine components, without thinking about what separates the two metal processes. Forging is the controlled deformation of metal into a specific shape by comprehensive force, a process evolved from blacksmithing. Casting is pouring liquid metal into a mold. The major differences between the two include strength, structural integrity, and resistance to impact and fatigue.
Grain Flow
A significant distinction of the forging process is the production of directional alignment, more commonly known as grain flow. Correct grain flow allows for the near absence of structural defects or voids common in the casting process. When metal is forged, the molecular structure of the alloy is forced to directionally align, giving the part more consistent strength qualities. In the casting process, the alloy molecules are free to settle where they please, creating a random grain structure, and opening up the potential for weak spots.
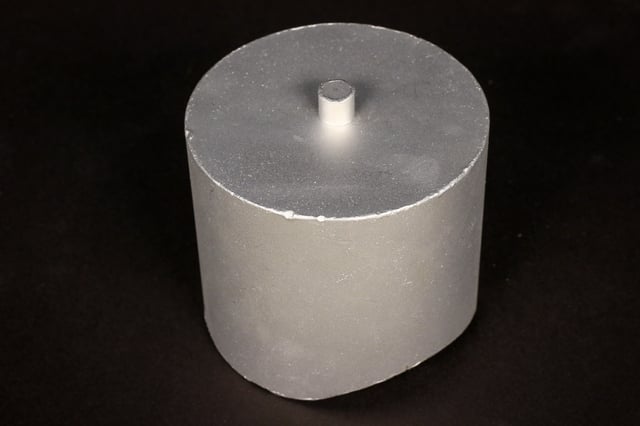
A simple analogy helps further explain the differences on a basic level: compare the forging process to making a table out of solid oak. The material is in its truest form, retaining is original aligned structure, making it very strong. Now compare the casting process to OSB (oriented strand board), a mixture of wood particles compressed together in an unoriginal form, making it pliable, but losing a lot of the wood's original strength qualities.
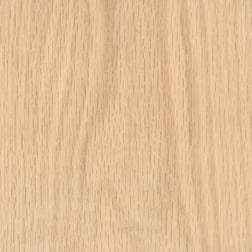
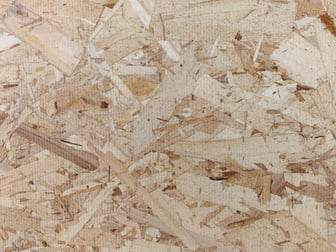
Forging's Long History
The ancient origin (as early as 4000 BC) of the forging process began in weapon design. Long before the development of engines, warriors used bronze and wrought iron to produce weapons.
Forged metal weapons began with a metal block that was heated to a specific temperature, then hammered, punched, or otherwise manipulated into the desired shape.
Unlike ancient times, modern forging is very specific. JE Pistons utilizes their in-house ISO 9000 certified forging facility, equipped with three mechanical forging presses and two isothermal hydraulic presses, along with their aerospace-grade heat treatment facility, to complete the entire process. Currently they are one of the very few aftermarket piston manufacturers in the United States with this advantage.
Forging Presses: Mechanical and Isothermal Hydraulic
The main differences between the isothermal hydraulic press and mechanical press are application-specific benefits. The key feature of the mechanical press is a high production rate. The force and speed are determined by the ram position, with full rated force only available when the ram is about bottom dead center. When pistons are forged via a mechanical press, the temperature of both the die and the puck must remain consistent and controlled throughout the process.
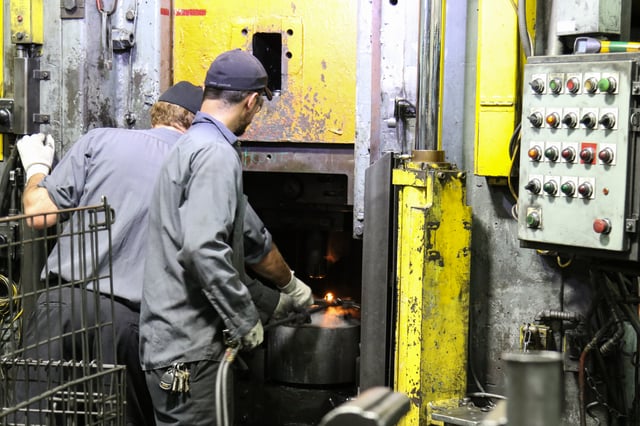
A major different with the isothermal hydraulic press is the use of computer numerical controls (CNC). Computer controlled features allow the press to have full rated force available throughout the full travel of the ram. Additional features allow the force and speed of the ram to be adjusted and controlled during the entire forging process, while also monitoring temperatures for easier consistency control. This method of forging is far leap from the ancient processes of heating and hammering metal, but the concept remains the same.
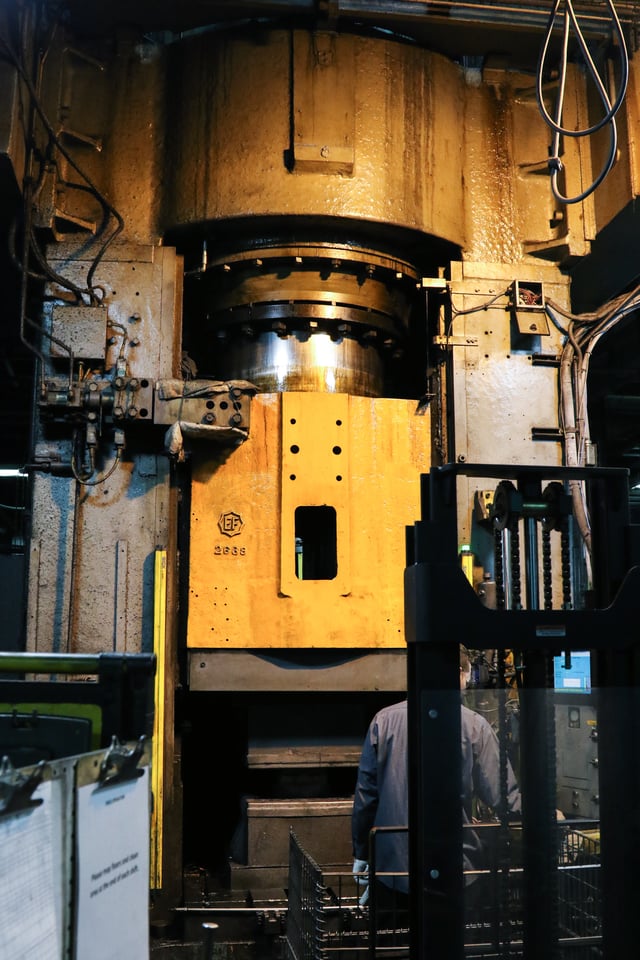
Post-Forging Processes
Forging pistons forces the material to flow and shape around the forging die, creating the base shape and structure of the pistons. After forging, the pistons do require a good amount of maching, including valve reliefs, skirts, ring lands, pin bores, and other undercrown features. This extensive maching is where the higher cost of forged vs. cast pistons comes from. JE Pistons are machined on a series of state-of-the-art CNC machines, allowing for very specific measurements and tolerances to be consistently met.
After machining is done, the forged pistons go through JE's aerospace-grade heat treatment, which is an equally important step to ensure the pistons deliver reliability beyond expectations. After this, some pistons may receive coatings, such as PerfectSkirt skirt coating.
Forging has a long history in creating alloy parts, and decades of innovation and new technology have led to JE's ability to create advanced and reliable forged pistons. New methods, techniques, and tweaks will continue to be tested and developed, to keep piston technology moving forward.